In the aerospace industry, there is little to no room for error, as even a small defect can lead to the total failure of the whole apparatus. Working in Aerospace Cleanrooms is one of the steps taken to reduce the chance of potential issues. In this case, contamination. Cleanrooms offer a controlled, contamination free environment, thanks to their use of filters and controlled air changes. The filters prevent air particulates from entering. These includes contaminants such as aerosol particles, dust, fungi, viruses, bacteria, and so on. The air changes are another measure of control present in a cleanroom, as they further help regulate air quality.
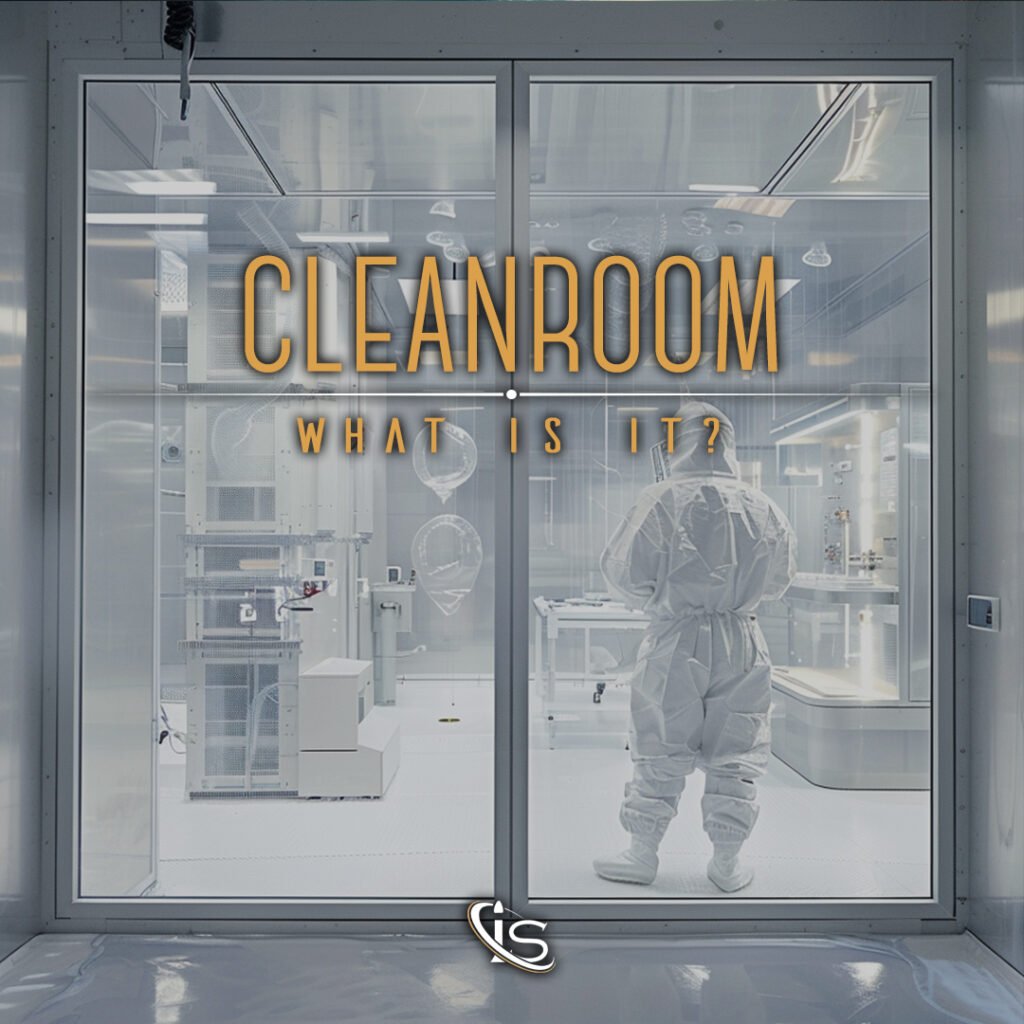
How Does a Cleanroom Work?
Cleanrooms are sealed rooms in which the air is controlled to meet a required specification. This specification is obtained by circulating the air through filters, typically ULPA or HEPA. These stand for Ultra Low Particulate Air and High Efficiency Particulate Air, respectively. The main difference between them is the density of the borosilicate fibers, with the ULPAs having a higher density. This leads to ULPA’s filtering 99.999% of particulates with a diameter of 0.12 microns or more, while HEPAs filter “only” 99.97%.
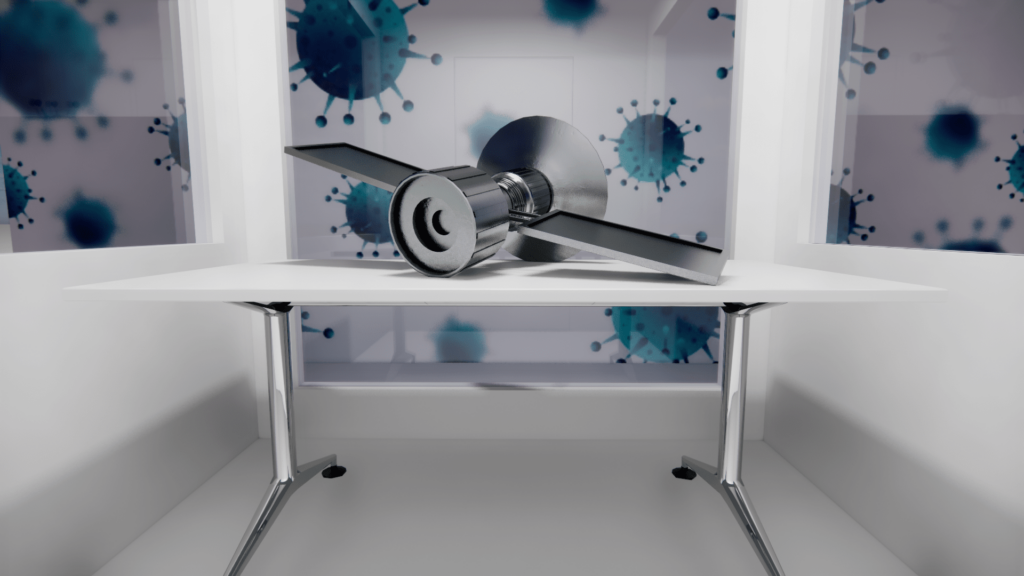
After passing through these filters, the decontaminated air is forced into the cleanroom. This decontaminated air can follow two different paths. The first has it pass into the filters again and restart the process in a so-called closed loop. The second, known as an open loop, has it forced out of the room, leading to the process starting anew with fresh air.
Beyond filters, there are, also, specific airflow patterns, designed to obtain the desired flow, humidity level, and ceiling fan coverage.
To avoid every source of contamination, the team working in the cleanroom needs to follow a set of rules in order to keep the room, well, clean. These include both their hygiene (e.g. the use of perfume and cosmetics) and attire — which usually includes the use of buffers, boots, overalls, goggles, and gloves.
Cleanroom Classifications
There are two different cleanroom classifications:
- The ISO, or International Standard Organization, classified the cleanroom into 9 different classes of contamination in the normative ISO14644-1; Class 1 represents the “cleanest” category and Class 9 the “dirtiest”. The air particle size determines the class of the cleanroom. In the aerospace industry the most used are Classes 7 and 8. To add some further context, Class 9 is usually equated to standard room air quality.
- The ASTM, or American Society for Testing and Materials, drew up a second classification, which deals, also, with the mechanical, thermal, chemical, and electrical properties of the controlled environment.
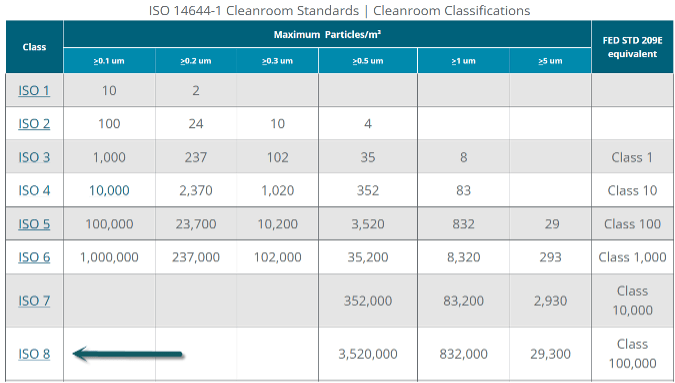
As stated before, the most used in the Aerospace industry is the ISO Class 8, also called 100.000 cleanroom after the maximum number of particles per cubic foot (PPC). Typically the air change rate here is between 5-48 exchanges per hour.
There are another two factors that get taken into account when classifying a cleanroom. The first, is airflow velocity. The greater this is, the higher the class of cleanroom it is associated with. For example, Class 1 has a velocity of 60-100 ft/min, while Class 8 has one of 1-8 ft/min. The second factor is the ceiling coverage. More specifically what percentage of it is covered by filters. Taking again the same two examples as before, we see Class 1 having 90-100% of its ceiling covered, while Class 8 sits at 5-15%.
Before ending this section, it is worth mentioning that ISO Class 5 cleanrooms are generally the cutoff for these environments having very strict environmental and contamination requirements.
Other Applications
All manufacturing that can be affected by contaminants uses a cleanroom, including pharmaceutical, medical, or nanotechnology. Every specialized task requires strict specifications and, therefore, different cleanrooms. For example, the ESA (European Space Agency) uses a cleanroom Class 1 to analyze temperature sensors destined for the Mars surface. The use of a Class 1 is rare, since very few Class 1 cleanrooms exist in the world.
And with that, we have come to the end of another capsule. “See you” all for the next one, right here, at impulso.space.