Welcome to another capsule on the aerospace industry. Today, we are going to discuss a topic we have treated in the past: cleanrooms. However, we are not going to focus on the classifications and requirements for these. Instead, we are going to discuss how exactly they are used in the industry and talk a little bit about Impulso’s very own cleanroom in our facility close to Cape Canaveral. But with the premise set, let’s jump into aerospace cleanrooms (after donning the appropriate attire, of course).

How Are Cleanrooms Used in the Aerospace Industry?
Each cleanroom has to comply with American Society for Testing and Materials (ASTM) standards. Beyond the classic parameters of limiting the number of small particles in the room and regulating the rate of air change, the standards for the aerospace industry involve some other restrictions. Some examples are the room’s ability to control thermal, mechanical, chemical, and electrical properties. These are especially important when considering the fact that aerospace cleanrooms often contain combustible materials (i.e. fuel).
In fact, the type of activity conducted within the room also affects what standards it must adhere to. Regulations are in place for almost all of the satellite preparation activities, such as handling and disposing of fuels, static control systems, payload integration, and more. Depending on the processes to be conducted, the standards can get even stricter than the typical ISO 8 cleanroom used in the industry. For example, the development of spacecraft hardware requires a higher classification of cleanroom than ISO 8.
Of course, not every cleanroom is devoted to just one type of activity. Some need to be able to support various facets of the industry, such as satellite manufacturing and assembly and packaging. However, the ones used for pre-launch activities tend to be made for those operations, specifically.
What’s Inside an Aerospace Cleanroom
The aerospace cleanroom can also contain varying equipment based on what operations are conducted inside. But there are some features that are standard to most. First off, all cleanrooms in the industry will feature either a HardWall or a RigidWall.
HardWall vs RigidWall Cleanrooms
HardWall is the most common type for aerospace, as it allows for an overall higher level of control. This is because a HardWall cleanroom is modular and prefabricated. It is also scalable, providing more flexibility and enabling it to adapt to various classifications. So, especially if the cleanroom is going to be used for spacecraft hardware development, or similarly sensitive operations, HardWalls will be better suited to reach the desired environmental control.
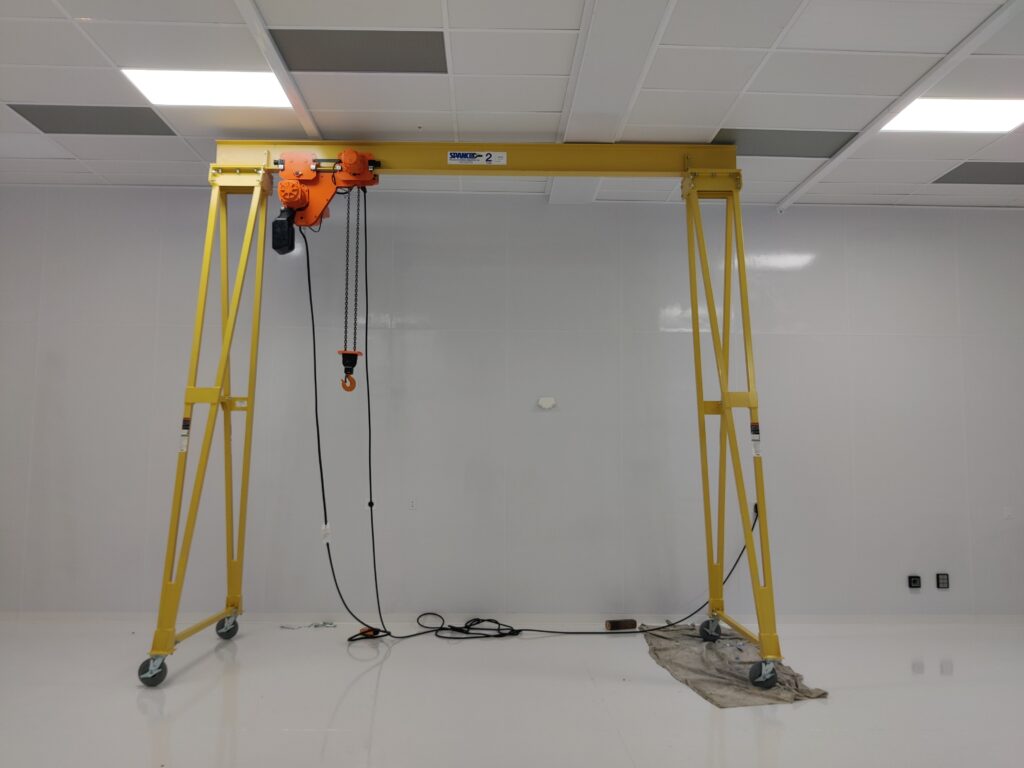
RigidWall cleanrooms, on the other hand, are still modular but made of transparent panels, instead of being prefabricated. While they may not be able to provide quite as much environmental control — particularly for the cleanroom’s temperature and humidity — they do offer other benefits. Mainly, the see-through nature of their panels makes them ideal for monitoring the equipment and payloads inside. So, for operations that do not require as strict of a cleanroom classification, the transparent RigidWall does offer a direct way to keep an eye on the inside.
Other Essential Features in Aerospace Cleanrooms
One of the most important features that an aerospace cleanroom must have is an HVAC system. Standing for Heating, Ventilation, and Air Conditioning, this is crucial to keep temperatures and humidity levels in the desired range. For aerospace operations, NASA recommends temperatures stay between 67-77°F. Humidity levels, on the other hand, should be between 30 and 50%. And while there are other elements that can help control these factors, such as airflow patterns or ceiling fans, a good HVAC is crucial for maintaining the conditions needed to work on delicate equipment.
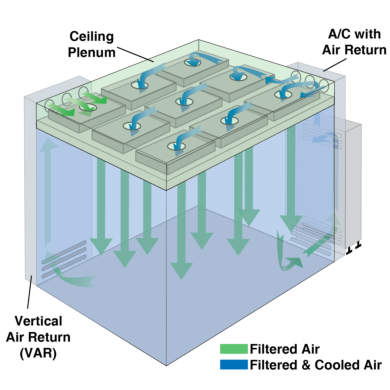
There are also other features that can be crucial for an aerospace cleanroom depending on its function. These include a fire suppression system, laminar flow systems, and fueling vents. Of course, there are even more pieces of equipment that can be used in a cleanroom for specific purposes. However, that really starts to fall on a case-by-case basis.
Impulso’s Cleanroom
As briefly mentioned before, Impulso has its own cleanroom, where satellite preparation activities can take place. With an ISO classification of 8, fueling vents, and both software and personnel security measures in place, our cleanroom can support a full launch campaign. In fact, D-Orbit has recently completed the first campaign to be ever fully done in our facility. Furthermore, its proximity to Cape Canaveral makes it the ideal place to store equipment between the completion of the campaign and launch.
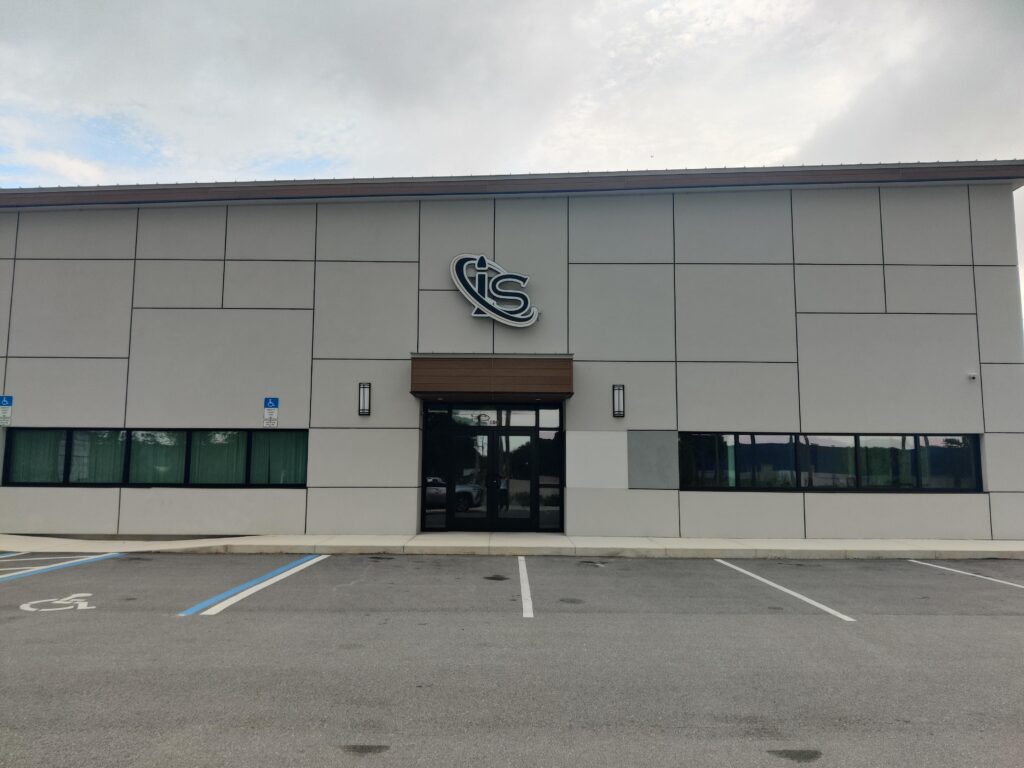
Thank you for joining us in exploring the world of cleanrooms once again. Hopefully, this capsule gave you a better idea of what a space needs to support satellite operations. Make sure to keep up with Impulso on social media to catch the next launch campaign involving our cleanroom!